What is polysilicon and how is it made?

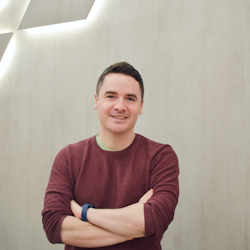

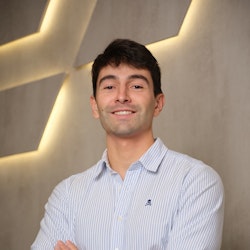
Gorka Arrieta
Product Owner
Gorka is an energy engineer turned Product Owner at RatedPower, and brings three years of experience in the renewable energy sector. With a fervent dedication to sustainability, he concentrates his efforts on advancing energy storage solutions that keep up with the fast developing pace of the industry. In his less than a year tenure at RatedPower, Gorka endeavors to contribute meaningfully towards a greener future.
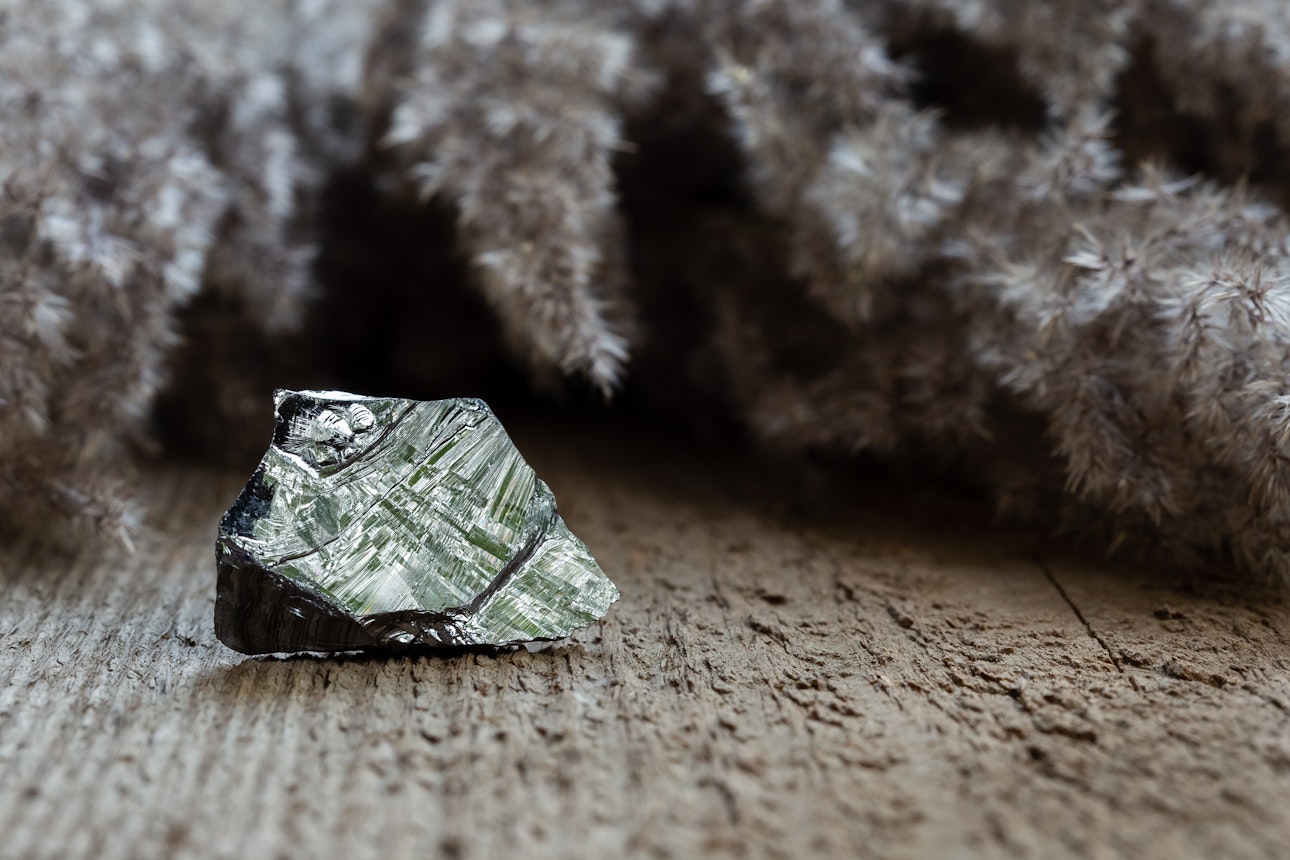
Read to learn more about polysilicon, one of the most important materials used in the solar market.
Content
What is polysilicon?
Polysilicon definition: Polycrystalline silicon, commonly shortened to polysilicon, is a purified form of silicon that includes p-type and n-type components. It is made up of multiple small silicon crystals which have been extracted from a rock type called quartzite, known for its high crystalline nature.
Polysilicon is highly pure and generates almost as much energy as pure mono-crystalline silicon. Because of this, polysilicon is crucial to the solar industry as it plays a key part when manufacturing solar cells that are used in solar panels. It is also used in various electronic devices from smartphones to automotive electronics.
How is polysilicon made?
There are two main methods to produce high-quality polysilicon that can be used for solar cell manufacturing: the Siemens process and fluidized bed reactor (FBR) technology. A third method — upgraded metallurgical-grade (UMG) silicon — was also in use for a short time. UMG utilized physical methods to purify the raw material of metallurgical-grade silicon such as vacuum melting and directional solidification of molten silicon, but these practices struggled to take prominence and were abandoned.
The Siemens Process
There have been many attempts to develop a less expensive alternative to polysilicon creation, but due to its refinement over the years, the Siemens Process remains the most common method used to create polysilicon.
First developed by German companies Siemens and Wacker in the 1950s as a way to produce hyper-pure polysilicon for semiconductors, the process has been carefully refined to bring polysilicon manufacturing costs down dramatically.
The Siemens process creates trichlorosilane (SiHCl3, or briefly TCS), a highly volatile liquid, as an intermediate product. This will remove the 0.5% to 1.5% of impurities contained in metallurgical-grade (MG) silicon.
MG silicon is ground up into small particles which react with hydrogen chloride (HCl). The resulting TCS has a low boiling point of 31.8C so it can be purified in tall distillation columns relatively easily.
The TCS deposits silicon on highly pure, slim silicon filaments that are electrically heated to up to 1,150C in a steel bell-jar reactor until they have grown to polysilicon rods with a diameter of 15 to 20 cm. This step is called chemical vapor deposition (CVD) and is the most energy-intensive part of the process. The long rods are then broken into small chunks.
The by-product silicon tetrachloride (SiCl4, or briefly STC) is recycled to TCS mostly through hydrochlorination: STC is fed along with hydrogen (H2) and MG silicon particles into the reactor for TCS production.
Different levels of polysilicon purity can be achieved through the Siemens Process. This depends on how thoroughly TCS is distilled and whether impurities on the surface of the polysilicon chunks are etched off. Expected purity levels for polysilicon manufactured through the Siemens method are as follows:
Solar grade for multi-crystalline cells (multi-grade): 99.99999% (7N) to 99.999999% (8N)
Solar grade for monocrystalline cells (mono grade): 9N to 10N
Electronic grade for semiconductors: 10N to 11N
Fluidized Bed Reactor (FBR) technology
Fluidized Bed Reactor (FBR) technology can be used to create granular polysilicon, but it has many drawbacks which prevent it from taking a larger market share, most notably:
The technology is protected by various patents
The complex fluid dynamics require significant time, experience, and capital to reach an industrial scale
The reactor wall requires a liner to avoid contamination, which increases building costs.
Despite its issues, there are benefits to pursuing FBR technology. FBR allows for continuous withdrawal of silicon granules, whereas the Siemens Process is interrupted when polysilicon rods are harvested.
A monosilane-fed FBR consumes just one-tenth of the electricity required to heat a conventional rod reactor used by the Siemens Process. However, the low electricity consumption can be offset by a high share of unusable silicon dust gathering in the output.
Mixing polysilicon chunks with granules from an FBR in a 50/50 ratio can shorten the time to fill a crucible by 40% and increase the charge weight by 30%.
How big is the polysilicon market?
The polysilicon market is recovering significantly after COVID-19 hampered production in 2020. Market demand quickly started to recover in 2021 and is expected to grow rapidly in the coming years. As of 2024, the polysilicon market is estimated at USD 14.49 billion. It is expected to reach USD 26.94 billion by 2029.
Despite the Siemens Process being developed in Germany, plants in China have adopted and refined the process significantly. This has led to China becoming the dominant nation for polysilicon production, accounting for nearly 80% of global polysilicon production in 2021.
Shortages and increased demand will likely see the market diversify over the coming years, with the US and Europe becoming more involved.
Polycrystalline vs. monocrystalline silicon
Polycrystalline silicon is the most common form we see in solar cell manufacturing, but monocrystalline silicon can also be used.
Monocrystalline panels are more efficient with a longer lifespan when compared to polycrystalline. They are also more effective in heat, which is helpful during the warmer months. However, monocrystalline is more expensive to produce and work with which makes it a poor choice for cost-efficient panels. Monocrystalline panels are also preferred from an aesthetic standpoint as they are black, allowing them to better blend in with rooftops.
Polycrystalline panels are cheaper to produce, but are significantly less efficient and have a slightly shorter lifespan than monocrystalline panels. They are also less efficient in higher temperatures. They are blue in color.
Choose RatedPower for your solar PV needs
Utility-scale solar plants will play an essential role in enabling the transition to green as countries around the world move to reduce their carbon emissions and address climate change.
We wanted to make this process easier and empower more companies to create effective solar PV plants with ease, ensuring a strong ROI. That’s why we built the RatedPower platform. The advanced data and analysis capabilities solar software provides enable project developers and operators to take advantage of economies of scale and maximize their return on investment. Watch our quick video demo to see how.
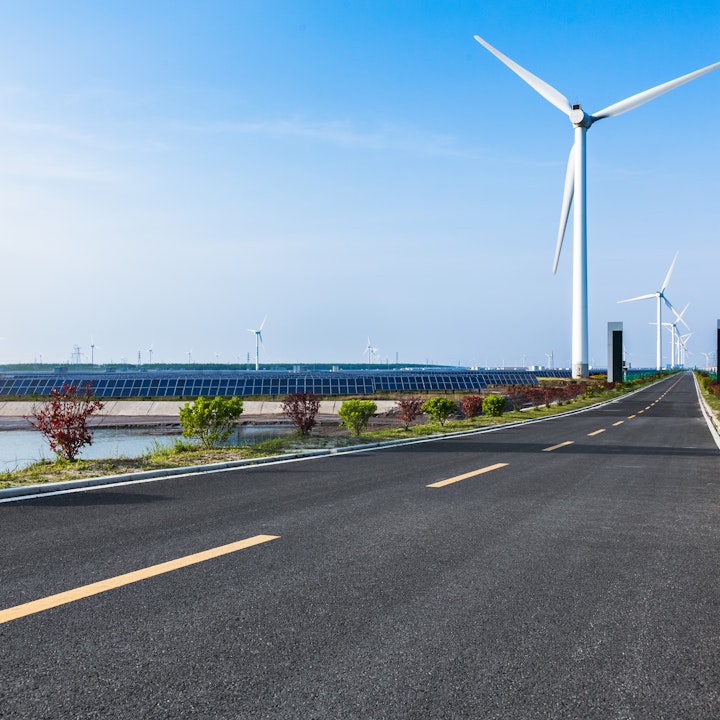
Design utility-scale solar at lightning speed
2024 Trends: Renewable Energy & Solar Research Report
Download our latest report to gather insights, stats, and opinions on the current state of the renewables sector. The report draws from an industry survey and analysis of solar simulations carried out on the RatedPower Platform.
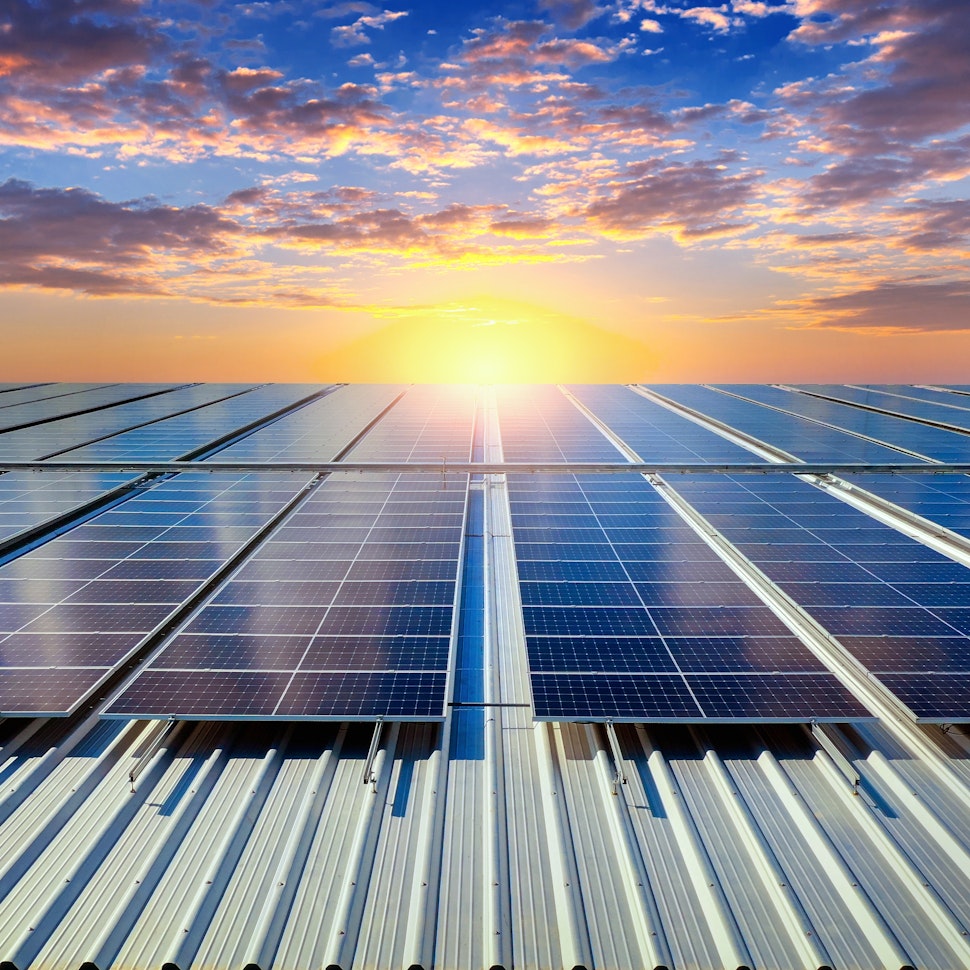
Latest stories
Related glossary posts
Market analysis
The importance of internal rate of return (IRR) in solar plant design
Updated 14 MAR, 24
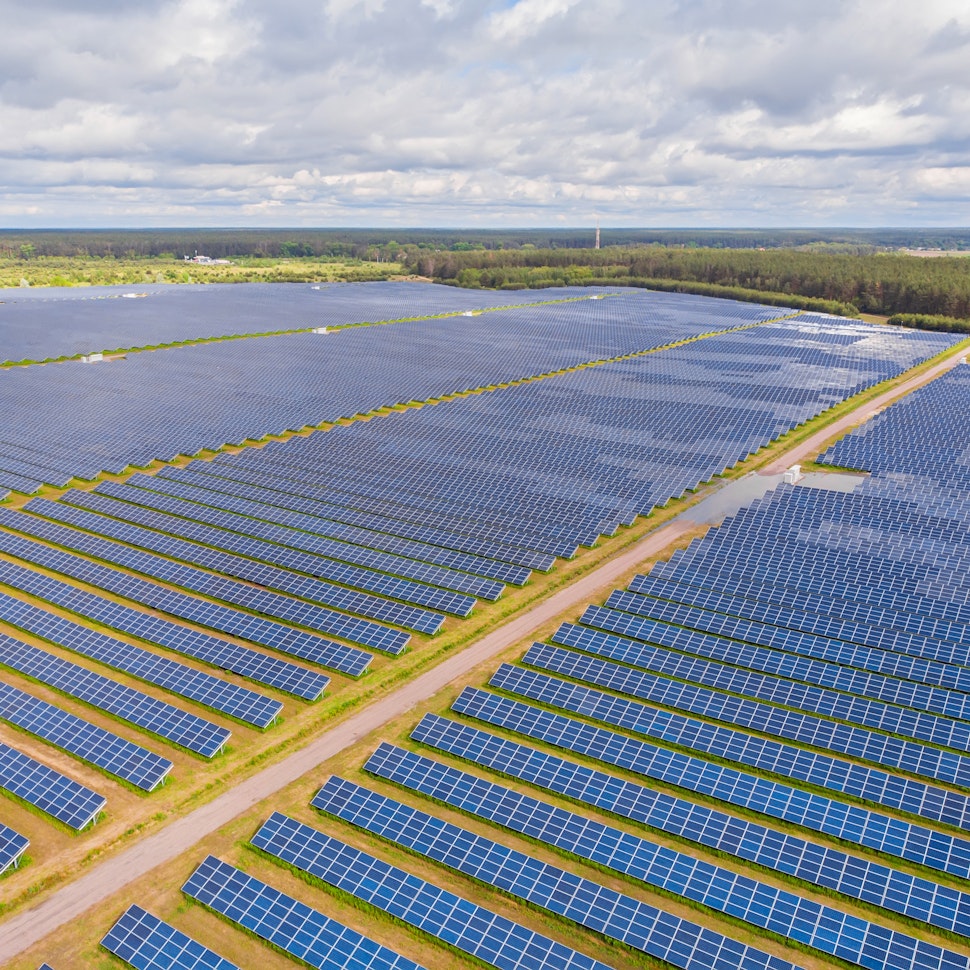
Market analysis
Understanding CAPEX and why it’s important for solar PV projects
Updated 13 MAR, 24
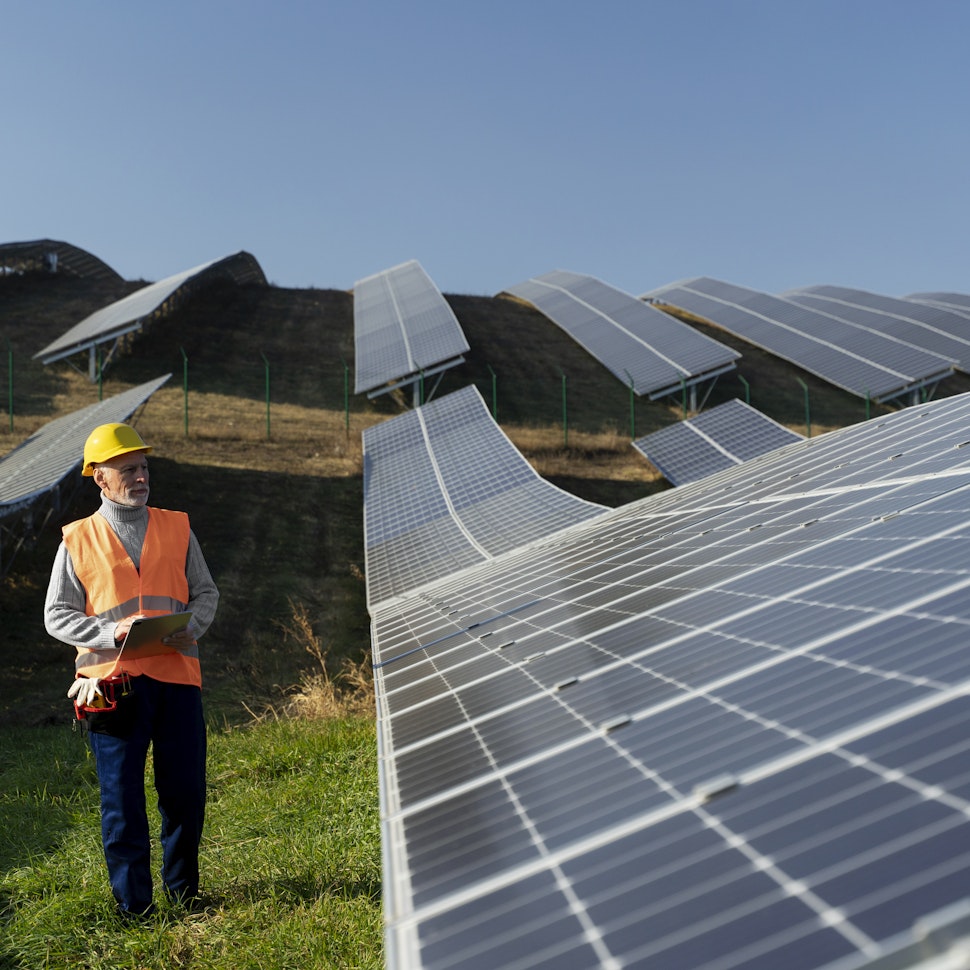
Related posts
Market analysis
Achieving solar growth in Iberia amidst connection challenges
Find out more about the structural roadblocks threatening to slow down Spain’s solar growth and how it can stay on track toward its clean energy goals.
Updated 26 AUG, 25

Market analysis
Navigating the UK’s Grid Reform: Opportunities and Challenges for Renewable Energy
Explore how the UK’s Clean Power Action Plan and grid reforms are reshaping green energy and creating opportunities for industry professionals
Updated 19 AUG, 25
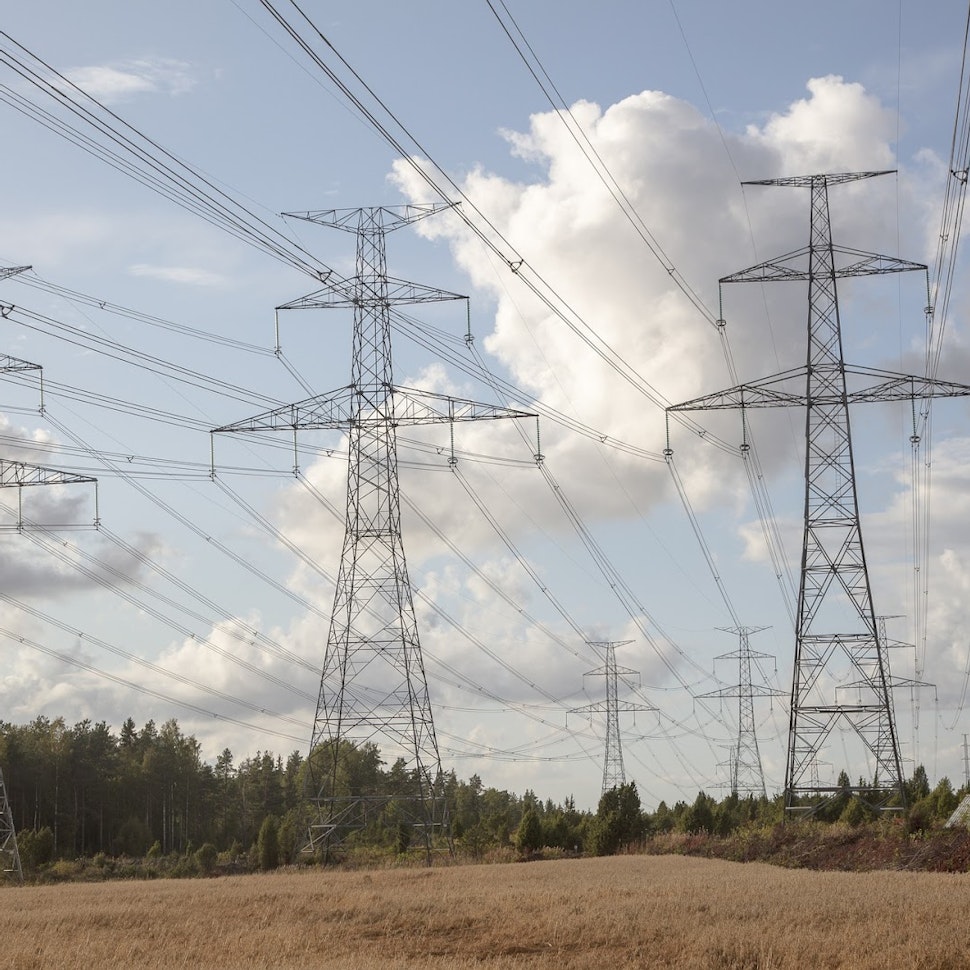
Market analysis
Exploring France’s grid and how BESS can reduce curtailment
France is scaling up to meet rising electricity demand, but grid constraints threaten to hinder progress. Learn how battery storage could unlock their clean energy future.
Updated 12 AUG, 25

- RatedPower
- Glossary
- P
- Polysilicon