What is an MV Cable and how is it used in PV power plants?

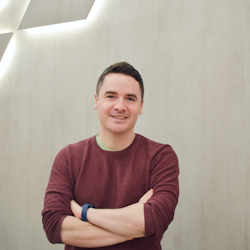

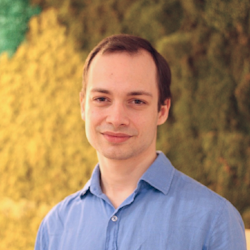
Álvaro Benito
Project Engineer and Software Developer
Álvaro is a Software Developer & PV Engineer with a background in Electrical and Electronics Engineering. He joined RatedPower’s Product team over a year ago, specifically the Interconnection team, where he's a key stakeholder on any AC-coupled storage, overhead line and substation-related initiative. In his current role, he is in charge of ensuring that the solutions delivered in RatedPower satisfy both the engineering and the software development requirements. Álvaro is analytical in his approach, and is adamant on making sure his team understands the technical reasons behind every new feature.
Content
MV Cable definition: A medium voltage (MV) cable is a commonly used and highly adaptable form of electrical cabling. It is used within commercial, industrial, and electrical utility industries thanks to its durability and flexibility.
The International Electrotechnical Commission (IEC) guidelines classify an MV cable with a broad voltage rating, between 1kV and 100kV. Actual voltage ratings of an MV cable will vary depending on the manufacturer and are more often seen between 3kV and 69kV. There is often overlap between the voltage ratings of medium voltage cables and high voltage cables, with an IEC60840 Standard High Voltage Cable being rated between 30kV and 150kV.
There are a lot of variables involved when choosing an MV cable, including construction, standards, voltage rating, and the materials used. Finding the right MV cable for your project will require research to find a cable that will balance performance, durability demands, and installation requirements.
What is an MV cable used for?
MV cables are usually designed with added protection in mind, so they can be used for a wide range of applications. We commonly see MV cables used for outdoor installations where weather conditions play a large part in the longevity of cabling.
Typical applications for MV cabling include:
Mobile substation equipment
Power distribution for industrial settings
Power distribution for tools and equipment used in mining settings
Maintenance and repairs, allowing for the downtime to be scheduled when needing to perform maintenance tasks or repairs
Wind farms
Solar PV plants
Public transportation infrastructures for supplying power to trains and metro lines
Weather-proof networks, allowing power to be transported underground so that severe storms do not disrupt the supply of power
Transformers
Medium voltage generator sets
Power distribution to isolated areas
MV cables come in various configurations and standards to suit different applications. Make sure to check that the MV cable you’re going to install is suited to the environmental challenges and performance requirements you need for your installation.
What are MV cables made of?
MV cables vary depending on the manufacturer and intended usage. There are many configurations available, with options for construction, standards, and materials used. There are also optional features, such as inner seething, additional armor, and water blocking. MV cables can be single-core, three-core, or single-core triplex.
Typically, an MV cable will have the following layers:
Conductor — This is made of either copper or aluminum to allow the electrical current to pass through the cable. Class 1 solid, Class 2 stranded (circular, circular compacted, sectorial)
Conductor screen — A semiconductive layer which helps maintain a uniformly divergent electric field and contains the electric field within the core
Insulation — Typically made of XLPE (Cross-linked Polyethylene) or EPR (Ethylene Propylene Rubber)
Insulation screen — Another semiconductive layer that protects against electrical interference, and also prevents the cable from causing electrical interference
Metallic screen — Copper wire or tape is wrapped around the core, or individual cores. This provides additional insulation and prevents electromagnetic interference
Outer sheath — This layer wraps around the entire cable to provide protection against environmental hazards. Typical materials used for an outer sheath on an MV cable include LDPE, MDPE (Low/Medium Density Polyethylene), PVC (Polyvinyl Chloride), and LSZH (Low Smoke Zero Halogen)
What is the difference between LV, MV, and HV cables?
For a while, there were only low voltage (LV) and high voltage (HV) cables. HV cabling was used for power distribution, while LV cables were used for nearly everything else. As the amount of electricity we use increased dramatically, so did the amount of power we had to send through cables. This meant new cable classifications needed to be created to better reflect which situations each cable type could be used in. We now have LV, MV, HV, extra high voltage (EHV) and ultra-high voltage (UHV) cables.
LV cables are still used for domestic, office, and other low-power applications, while industries requiring more power have a range of options from MV cables to UHV cables.
Each type of cable will carry a different voltage. Typically the voltage rating of each cable type is as follows:
LV cables have a voltage rating between 300V and 1000V
MV cables have a voltage rating between 1800V and 30kV
HV cables have a voltage rating between 36kV and 150kV
EHV cables have a voltage rating between 89kV and 400kV
UHV cables have a voltage rating above 400kV
Most cable types are then split into smaller categories and voltage ratings can vary depending on usage and manufacturer. For example, MV cables often come with a voltage rating of 36kV to 66kV. Make sure to check the exact voltage rating when selecting a cable for your installation.
MV cables for solar PV installations
MV cables and solar PV installations go hand in hand. An MV cable is the perfect choice when it comes to interconnecting your power stations at the site and sending the power down to the local substation.
It’s important to consider the routing and grouping of MV cables within a solar PV plant. The goal is to reduce the length of cable required, limit energy loss, and allow for easy maintenance to reduce costly downtime.
This is something we have considered at RatedPower. We want to make it as easy as possible for engineers to design highly effective PV plants and reduce LCOE. RatedPower software allows you to fully customize MV routing between areas and the step-up substation, while our algorithms take the defined path and transfer the settings between the layout design, the bill of quantities, and the technical documentation.
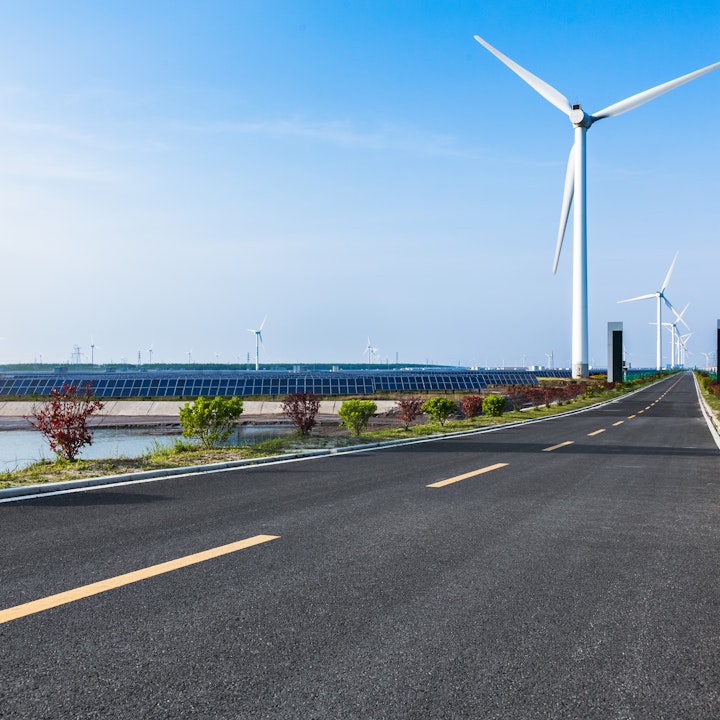
Design utility-scale solar at lightning speed
Plotting Your Overhead Lines with pvDesign
Download the guide to take a deeper look at overhead lines and learn how to incorporate them into a utility-scale project using pvDesign.
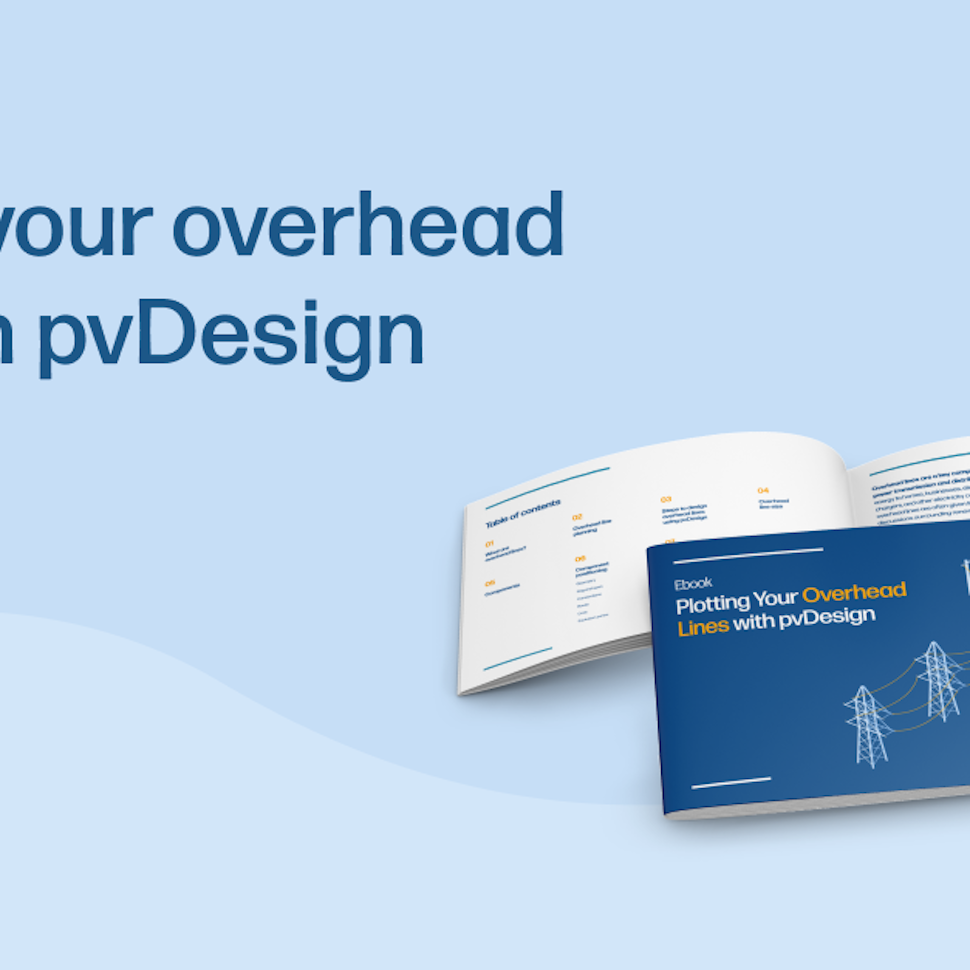
Latest stories
Related glossary posts
Technology and engineering
What is a solar substation and how to customize yours with RatedPower software
Updated 5 MAY, 25
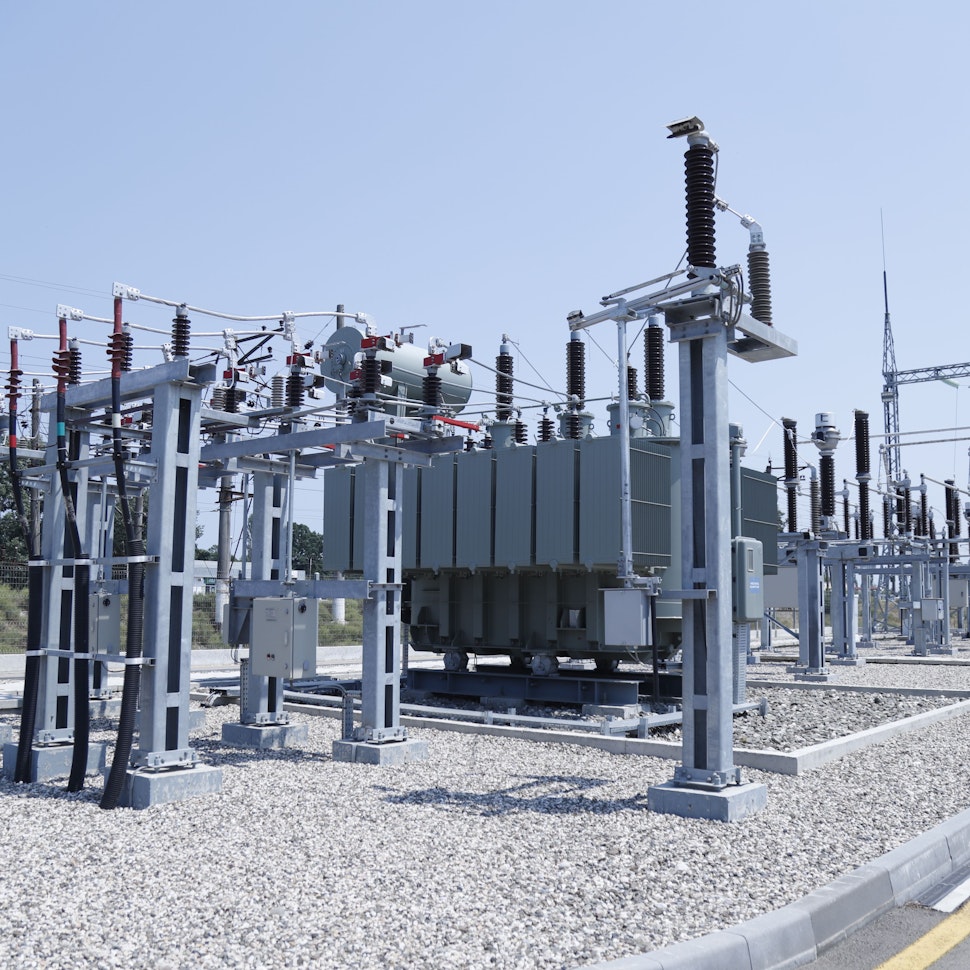
Technology and engineering
What is a solar combiner box and why is it used in photovoltaic designs?
Updated 25 MAR, 25
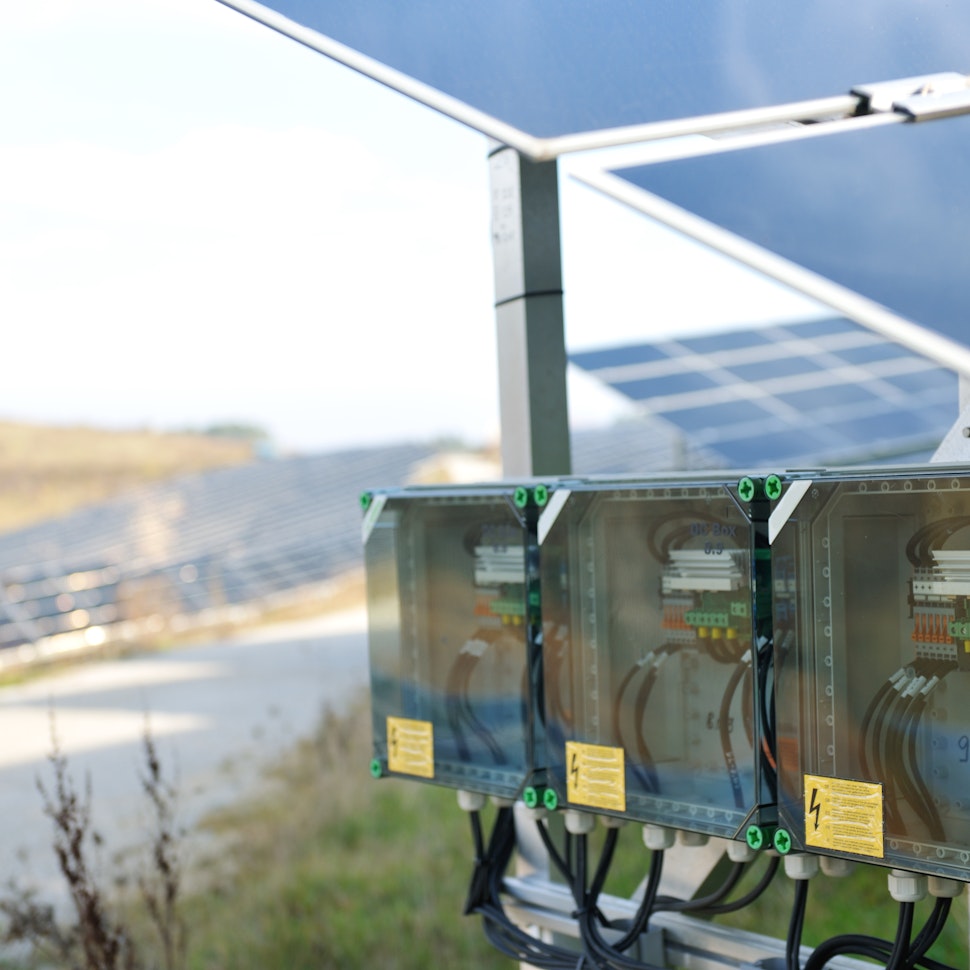
Technology and engineering
What are the benefits of a Power Purchase Agreement (PPA) for solar plants
Updated 25 MAR, 25
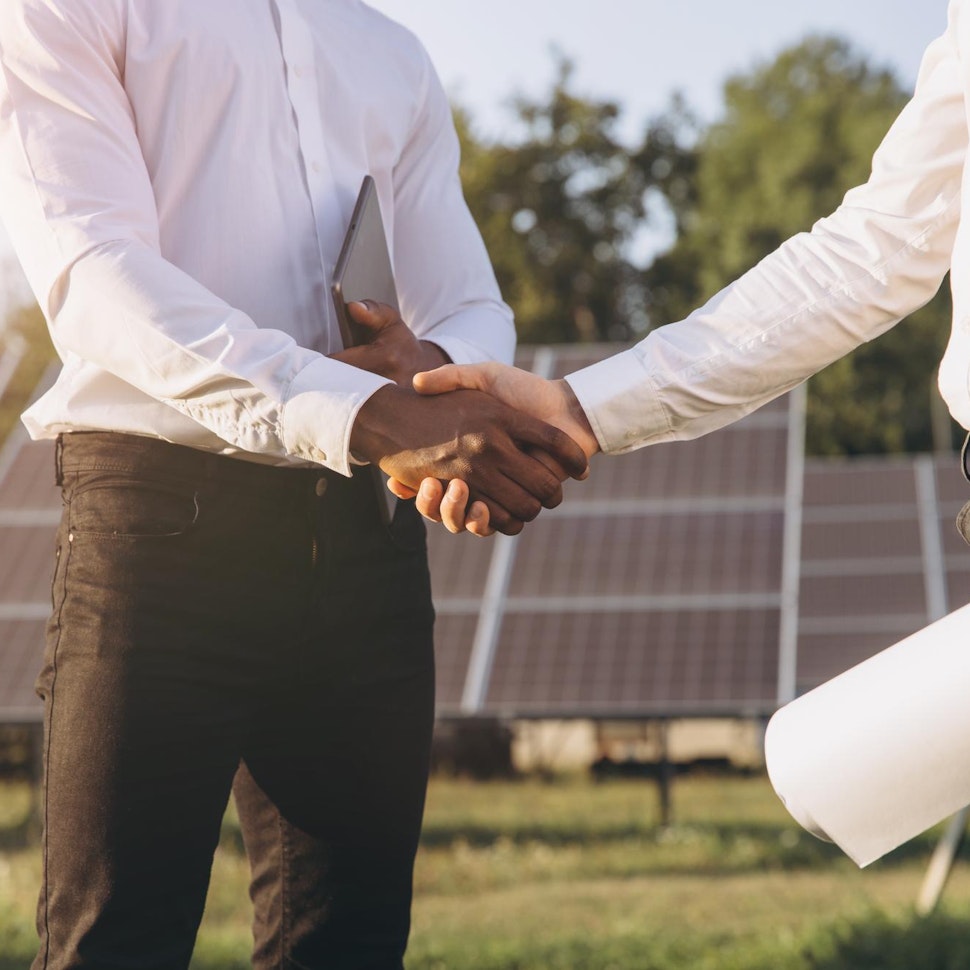
Related posts
Technology and engineering
The green hydrogen boom in LatAm
Latin America is emerging as a green hydrogen leader. Learn how LatAm countries are leveraging solar and wind power to drive green hydrogen production.
Updated 22 JUL, 25
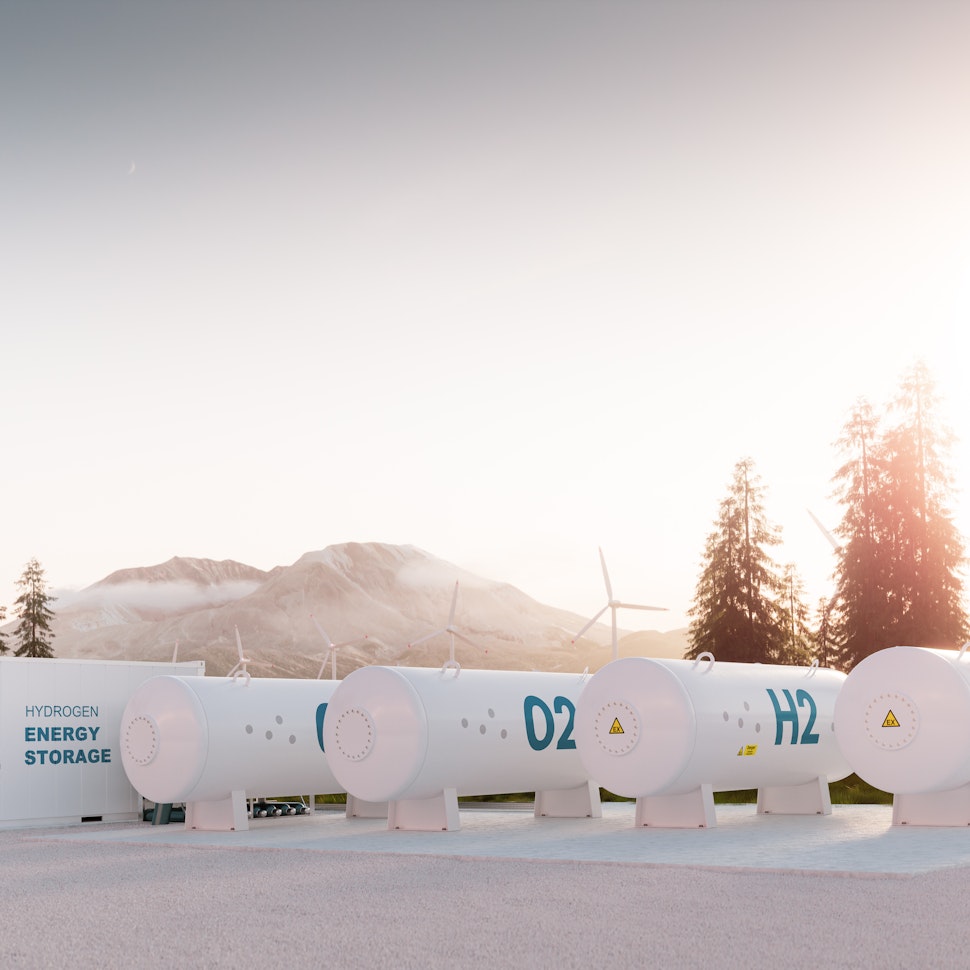
Technology and engineering
Innovation in renewable energy: Developments expected in 2025
We look at the 10 biggest renewable industry developments that are making a green future possible, including perovskite solar cells, green hydrogen, and more.
Updated 18 MAR, 25
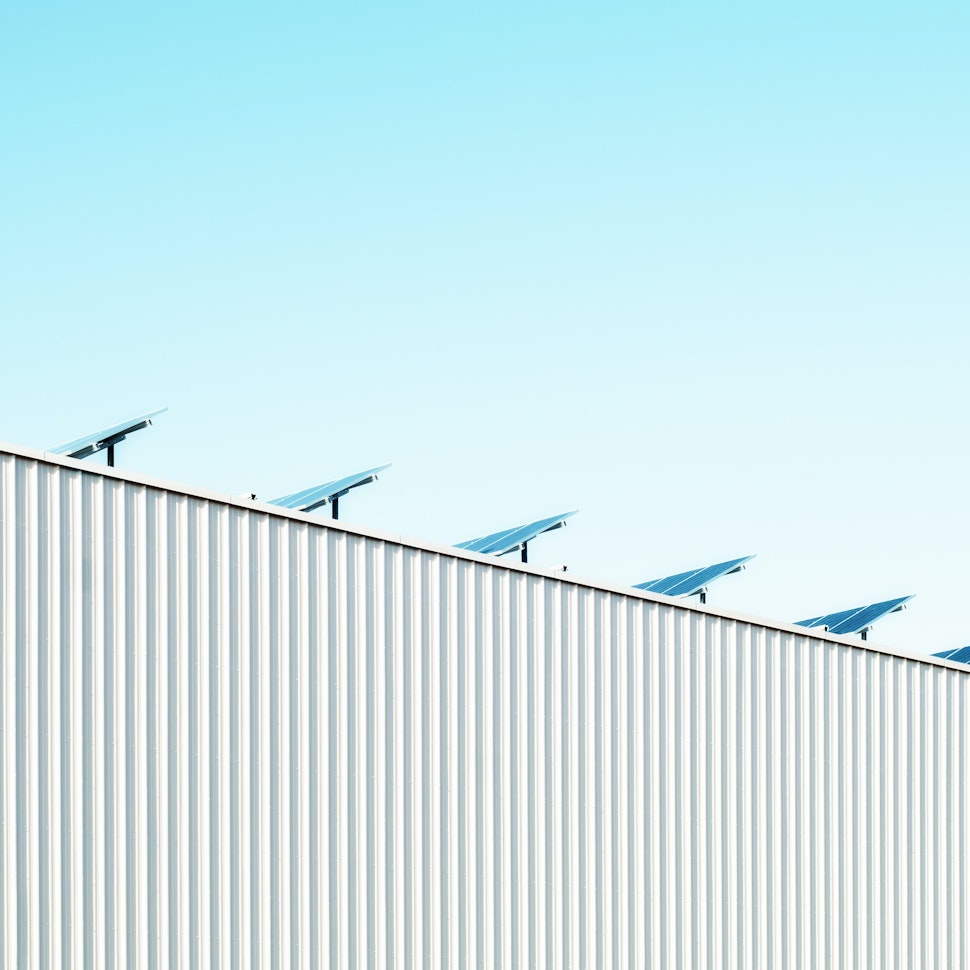
Technology and engineering
What the future holds for the longevity and efficiency of solar panels
Tests done by the French photovoltaics group Hespul showed that the panels, installed in 1992, are still operating at an astonishing 79.5% efficiency. Read on to find out more.
Updated 4 MAR, 25
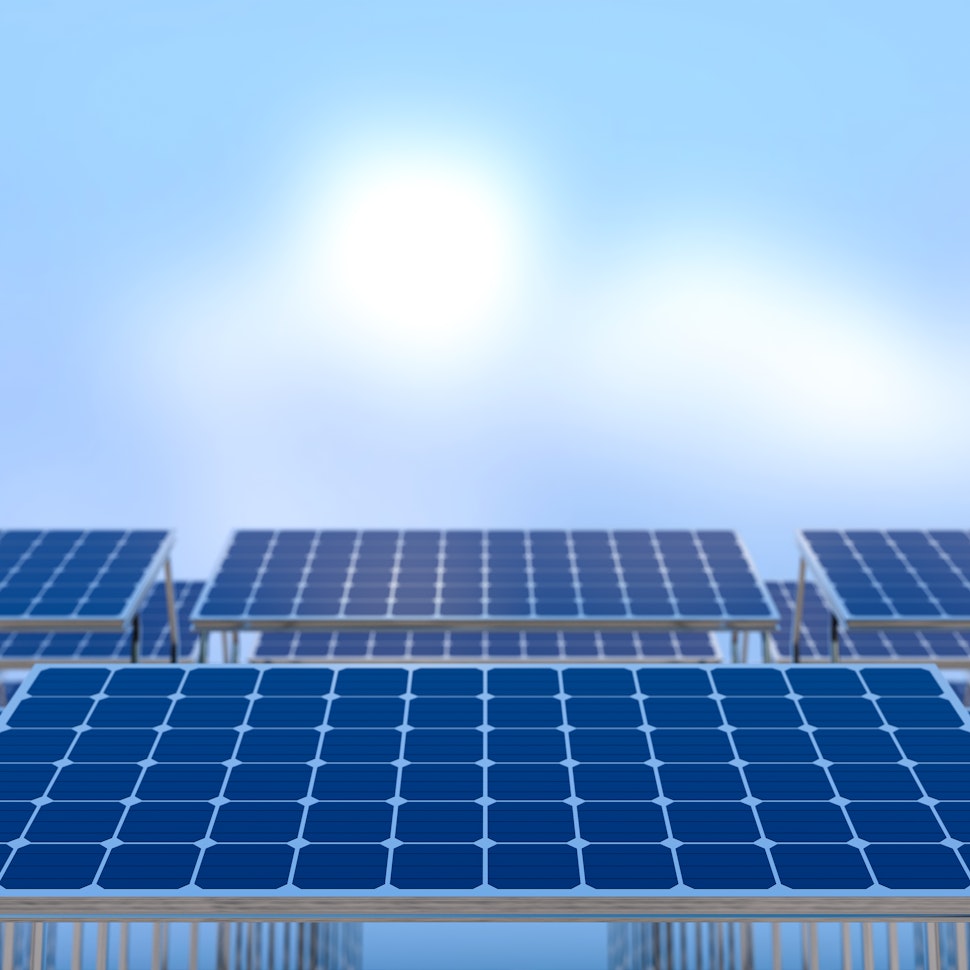
- RatedPower
- Glossary
- M
- MV Cable